September 22, 2023
Just a few steps away from the Offshore Oceanographic Science Vessel under construction at Vancouver Shipyards, you will find Seaspan’s Welding Centre of Excellence. Inside the industrial space, there are rows of welding booths used for welding training and development. Look to the left, and you’ll notice something more unusual to a shipyard: a fully enclosed science lab.
To learn more about the Centre of Excellence Lab, and its role in helping Seaspan create efficiencies to prepare to build a Polar Icebreaker, we sat down with Hassan Saghafifar, PhD, PEng.
First, let’s meet Hassan.
My name is Hassan, and I am the Welding Specialist at the Centre of Excellence lab at Vancouver Shipyards.
I started my career path in Iran, where I graduated and worked in the oil and gas industry. I then moved to the UK, where I obtained my PhD, and gained experience in a Materials Testing lab environment. Finally, my family and I moved to Canada before I decided to join Seaspan in February 2020 to establish this Materials and Welding lab.
It’s been an exciting journey, and I’m proud to share more about how the Centre of Excellence lab is driving innovation at Seaspan.
What is the Centre of Excellence lab?
The Centre of Excellence lab is a CWB certified facility stocked with cutting-edge scientific equipment for mechanical testing and chemical analysis. It is located inside the Centre of Excellence building on-site at Vancouver Shipyards.
What are the main objectives of the lab?
The main purpose of the lab is to perform mechanical testing which is required for the qualification of our welding procedures, and as a space to research and develop new welding techniques and processes for use in the shipyard.
We are currently in the process of developing specialized welding procedures for the Polar Icebreaker project involving a higher grade of steel that maintains high toughness at low arctic temperatures.
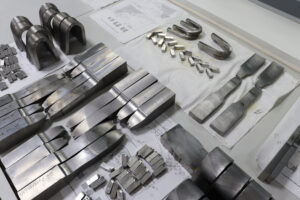
Various tests are run on steel samples to ensure they meet the required standards. The samples above are impact, tensile, and bend samples using polar project grade steel
How has your role changed over time as the Centre of Excellence lab has evolved?
When I first joined Seaspan in February of 2020, I was primarily involved in designing the lab and purchasing the required equipment.
Over the past year, I’ve shifted my focus to installation and calibration of equipment. The final step in setting up the lab was obtaining CWB certification. Having CWB certification means that we are fully certified to perform tests on-site for new projects like the Polar Icebreaker.
What are some of the lab’s capabilities?
Before starting to weld in the yard, we need to run mechanical tests to prove the quality of the weld. With cutting edge equipment and a skilled team, we can run charpy testing, tensile testing, hardness testing, and chemical composition testing.
How does the Centre of Excellence lab tie into the Polar Icebreaker project? Why are we starting this work now?
One of the ways that we are getting ready to begin production on the Polar Icebreaker by 2024 is through our work on the polar prototype block. The testing currently taking place in the Centre of Excellence lab is another way we are prepping and preparing our systems for Polar, and the timeline requires us to start the testing process now to drive efficiencies as we prepare for the build.
To set the stage, let’s keep in mind that Seaspan is currently in the design and engineering phase of the project, with plans to deliver the Polar Icebreaker in 2030. From a welding engineering perspective, one of the challenges of the polar project is the thickness of the steel, which is up to 60mm. We are also dealing with a different grade of steel.
This is where the Centre of Excellence lab comes in, because we need to test run all our welding procedures on this new kind of steel. Having this kind of a lab in-house means expanding our internal capabilities, it saves time, while putting us on a trajectory of improvement.
Can you expand a little more on that? What are some of the benefits to having an on-site lab?
There are several benefits to having an in-house lab. First, we can reduce turnaround time by having tests done right here at Vancouver Shipyards instead of sending samples to a third-party lab, which can add several weeks to the process. Especially if a test fails – the turnaround time for re-testing internally is much faster. We also have the unique opportunity to run some mechanical testing in-situ with our procedure development. Finally, a significant benefit is our CWB certification. It means we can be relied on to carry out the job right, and to the highest quality standards.
Looking to the future, this could create opportunities to deliver our services to different customers, including other shipyards under the Seaspan umbrella, like Victoria Shipyards, as well as external companies. My team and I are very proud of the work taking place in the Centre of Excellence lab, and we’re excited to continue to support the Polar program and beyond.
Thank you, Hassan, for sharing your knowledge with us! Check out the photos and stay tuned for more updates about polar progress and what’s happening behind the scenes in the Centre of Excellence lab.
Behind the scenes at the Welding Centre of Excellence lab